Width | Size(mm) | ||
S | r±0.1 | L | |
200 | 2.0 | 0.2 | 21 |
300 | 3.0 | 0.4 | 21 |
400 | 4.0 | 0.4 | 21 |
500 | 5.0 | 0.4 | 26 |
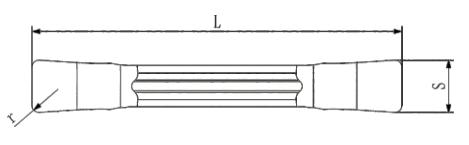
Product name: MGMN insert Series: MGMN Chip-Breakers: M/G
Width | Size(mm) | ||
S | r±0.1 | L | |
200 | 2.0 | 0.2 | 21 |
300 | 3.0 | 0.4 | 21 |
400 | 4.0 | 0.4 | 21 |
500 | 5.0 | 0.4 | 26 |